Home » Uncategorized
Category Archives: Uncategorized
Ultrasonic Impact Peening
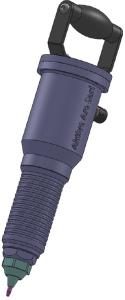
In 2004 we were approached by a client specialized in Life Extension of mechanical assemblies and parts.They asked for a customized Ultrasonic Impact Peening system to be used for the treatment of welds and metal parts surfaces. The principal application was to treat critical weld joints in Offshore Oil Production Structures and Vessels. As these very expensive facilities reach their defined end of life there are clear signs of damage due to the normal stress and strains of the offshore environment. Inspection of weld joints in high-stress areas were showing clear signs of damage to welds that were cracked and had rust forming in these crack areas.
Operators of these offshore structures are faced with the difficult question of maintenance, the high cost of production downtime, and the eventual very high cost of replacement. One practical and cost effective solution is Ultrasonic Impact Peening treatment of critical zones. The work can be done during normal inspection periods and in many cases will reset the life of a weld to zero allowing up to 10 years of additional life. This kind of maintenance will is extremely cost and time effective not only for maintaining welds but also offering a significant saving in lost production time and more importantly extending the life of a very costly structure.
Over the past 13 years we have continually improved our Ultrasonic Impact Peening system design and developed some proprietary technology to make our systems more reliable and flexible. If you have any application that you believe can benefit from Ultrasonic Impact Peening please contact us to discuss how we can help.

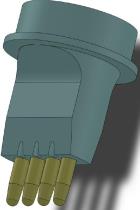
Visit our Applications Page for more detials: https://www.aaultrasonics.com/ultrasonic-impact-peening/
Nono Particle Ultrasonic Dispersion and Atomizing
15 January 2016
Aktive Arc Ultrasonics Group delivers key technical solutions enabling uniform nanoparticle surface coating of medical materials.

Our client, a medical devices manufacturer, presented two challenges: 1) make uniform dispersion of nanoparticle in a liquid and eliminate agglomerates; 2) improve spray coating of the nanoparticle loaded liquid.
Problem 1)
Conventional stir mixing of nanoparticles into the carrier fluid did not provide sufficient dispersion. Even with rigorous and long mixing cycles agglomerations of nanoparticles remained.
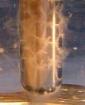
Solution 1)
Ultrasonic mixing is a well-known and proven technology for dispersion of nanoparticles in a liquid. We designed a custom and proprietary ultrasonic mixing flow cell as a final mix stage that allowed continuous processing and delivery to the atomizing assembly. In this application a high intensity sonotrode with a diameter of 30 mm was used. Such sonotrodes can provide a combination of strong cavitation on the end tip and along the side surface.
Problem 2)
Conventional air pressure spray nozzles do not offer sufficiently small droplets for this application and the air pressure spray system creates a wide spray pattern resulting in significant overspray and wasted material.
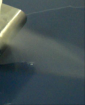
Solution 2)
Ultrasonic atomizing is a very efficient technique for making an extremely low pressure spray with a focused pattern and the particle size can be targeted by using an appropriate ultrasonic frequency. When sufficient vibration amplitude on the end tip of the sonotrode is achieved a liquid applied to the tip will atomize on contact. The resulting atomized cloud of droplets has extremely low pressure and the cloud pattern can be customized by shaping the sonotrode tip. Depending on the ultrasonic system frequency the atomized liquid can have a target particle sizes in the range of 15 micrometers to 100 micrometers.
The delivered system met the client’s requirement for nanoparticle dispersion and target spray particle size in a spray pattern that significantly reduced material waste.
© Aktive Arc Sarl 2015